Meet Steve Hodge: award-winning CTO of Versarien and graphene industry champion
Applications Collaborations Graphene Engineering Innovation Centre Research 6 September 2022
Recently named ‘Rising Star in Industry’ by the Royal Society of Chemistry, Versarien chief technical officer Steve Hodge plays an influential role across several graphene working groups, looking at the challenges of commodification and supply-chain adoption for 2D materials. We sat down to discuss emerging prospects for the market in a wide-ranging interview...
How have you seen the graphene industry maturing over the past 3-4 years and how has Versarien being part of the Graphene@Manchester ecosystem helped?
Being part of the Graphene Engineering Innovation Centre (GEIC) community at The University of Manchester is incredibly important to Versarien. It gives the company an additional strength: graphene was first isolated in Manchester in 2004, it’s the home of graphene, and often that’s a great starting point for customer conversations.
The GEIC was established in 2018 and Versarien was the first to join. So, right from the start, we have been part of the GEIC Technology Advisory Board, had access to dedicated GEIC laboratory space, and have been able to use state-of-the-art equipment in the centre’s facilities.
Over the last three-and-a-half years, we have been able to use these facilities to test new ideas and products and scale up products to take to market. Initially, our activities were focused on graphene-enhanced carbon-fibre composite materials, but that’s since widened to projects on coatings, textiles, printed electronics and energy storage. So it’s giving us that toolkit to develop and test our materials in wide-ranging applications.
It’s also opened the door to other companies, which has helped us become part of supply chains as a materials producer and application developer.
What are the main sectors Versarien is looking at for near-term commercialisation and what are the barriers still to overcome?
Construction and textiles are two key sectors that we’ve seen really transition over the last couple of years. Both industries have lots of potential for the use of graphene and the benefits to customers are huge. Additionally, both sectors need high-performance materials and they’re also increasingly driven by their carbon footprint and sustainability. As a business, we have a clear strategy to penetrate the concrete and textile industries and have developed products in both (CementeneTM and Graphene-WearTM).
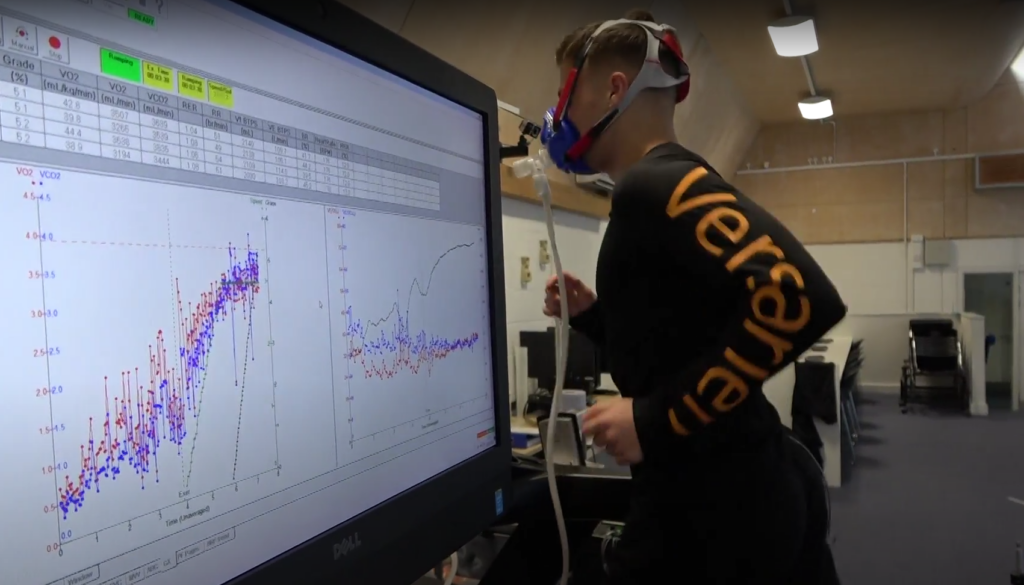
The main barriers for these industries now are the regulation and standards needed and getting products to market following Brexit. In some cases products need to have the UKCA (UK Conformity Assessed) marking and the CE marking for Europe to ensure they fully comply with both EU directives and UK regulations. At Versarien, we have been through this process with our FFP2 RD graphene-enhanced face masks back in 2020, which are CE-marked, meaning they satisfy the legislative requirements to be sold.
For the textiles sector, we’ve registered our materials on the ZDHC portal (zero discharge of hazardous chemicals) and are now pursuing other industry certifications. In the construction industry, we are pursuing other standards and certifications, but it’s not a quick process. They can take many months to go through, but we’re pushing as hard as possible to accelerate the process.
Environmental sustainability is increasingly central to procurement across industries including construction, aerospace, automotive etc. but green solutions are traditionally expensive. How can graphene help?
There’s a misconception that graphene is very expensive and that it’s still not being produced at sufficient scale to be adopted by industry. But companies are now seeing prices of traditional raw materials increasing, for example, plastics companies are being charged more tax for using fossil-based materials, so sustainable alternatives are firmly on the agenda for companies needing to address these concerns.
This, combined with other external factors, such as the ongoing crisis in Ukraine, means prices are going up, so the consequence of graphene being slightly more expensive – albeit the price of graphene has fallen dramatically in recent years – is having much less of an impact. The gap is closing and graphene can be adopted as a cost-effective material.
Looking at sustainability and the environment, there are several applications where graphene can help the environment. At Versarien, we’re tackling the construction industry which, like many other industries, has come under scrutiny for its massive carbon footprint – it contributes to 40% of the UK’s carbon emissions.
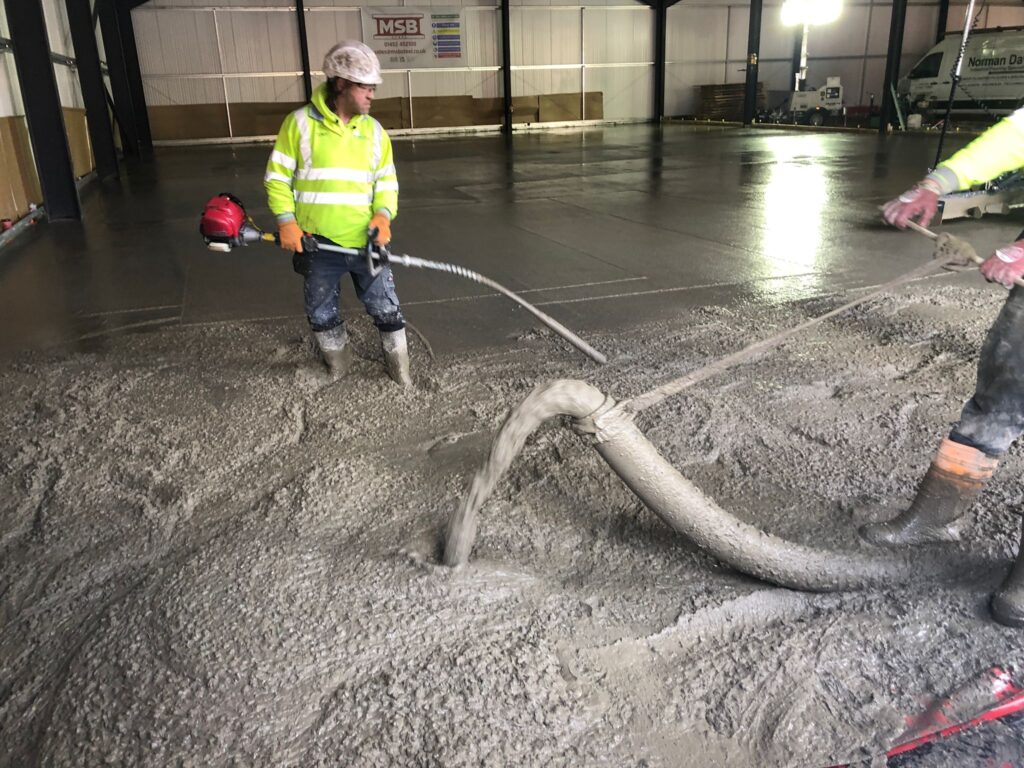
To get away from using so much cement, we are able to add small amounts of graphene material in a form of a water-based admixture – Cementene TM. The dosage is so small that the uplift in the graphene cost is outweighed by other material savings and lifetime benefits. Graphene, made of carbon, and typically produced from graphite, is one of the most abundant materials on earth, so it is unlikely to become scarce. The impact on construction means that fewer materials are used, increased cost efficiency, and reduced carbon emissions.
Any other priorities for Versarien on sustainability?
Another critical area is polymers. Polymers are a great invention. They have many functions, and we shouldn’t completely switch off from using oil-based materials for plastics. But we need to focus on reuse and recyclability and what graphene can do to these kinds of materials. We’ve seen the ability to use 20- 50% recycled content by adding graphene to fossil-based polymers, and we’re hoping to push that to other recycled materials. That would considerably impact sectors such as the textiles industry, where ‘fast fashion’ is causing significant issues with the rate at which clothing is being bought and thrown away.
The benefit we’re seeing with graphene is that it enhances mechanical performance at low loadings, which leads to better durability and longer lifetimes of products.
Every industry has challenges and graphene can offer something to every industry. Now it’s about educating customers on what can be done and showing the data on what can be achieved with graphene-based materials rather than ‘green-washing’. We often talk about ‘lots of potential’, saying graphene can offer material and CO2 savings, but now we need to deliver and showcase the results to date.
You sit on a couple of working groups around REACH (Registration, Evaluation, Authorisation and Restriction of Chemicals). What influence do these have and how do you see regulations evolving?
We’ve been REACH compliant since 2019. REACH was adopted to improve the protection of human health and the environment from the risks that can be posed by chemicals and impacts the whole supply chain. Every chemical manufactured/imported at more than one tonne per year must go through the process of submitting certain physicochemical data, toxicological and ecotoxicological information.
Currently, as an industry, individual businesses can manufacture and export up to 10 tonnes of graphene annually in Europe. That’s for the bulk powder form, so you could, for example, put 10 tonnes of that graphene into 1,000 tonnes of a polymer to make composite materials.
To get above different thresholds of 10, 100 and 1,000 tonnes per year compliance, you have to do longer-term studies, which could involve looking at the interaction of graphene in soils and effects on plant species and studying long-term effects that might lead to cancers and other genetic mutations. The potential for animal testing exists, although these are always a last option.
“Every industry has challenges and graphene can offer something to every industry. Now it’s about educating customers on what can be done and showing the data on what can be achieved with graphene-based materials rather than green-washing”
Post-Brexit, we now have UK REACH, and we’re one of only a few companies that are on the path to being compliant for both UK and EU REACH. And that’s evolving because other territories like South Korea and Turkey are also adopting REACH. So, we must adhere to different deadlines to register our materials if we want to sell them or manufacture them in these other territories.
Regulations and methods of testing will certainly evolve. New tools and protocols are being developed specifically for nanomaterials such as graphene, and once adopted, could assist in the regulatory processes and provide more confidence to the supply chain and the consumer.
How does it work in practice? Do you liaise individually with REACH and do your own characterisation work?
In practice, graphene manufacturers have come together and formed a “Graphene REACH registration consortium”, managed by an independent party. Ten companies are currently registered for the substance ‘graphene’ with a set of parameters that define these materials following companies submitting their own physical and chemical characterisation data.
Because the materials manufactured are relatively similar, we can use a material from one company to carry out a toxicological test. Those tests are conducted by global test agencies performing the measurements, following OECD (Organisation for Economic Co-operation and Development) guidelines and with Good Laboratory Practice principles.
A lot of research has been done previously by academics and shows the potential safety or risks of graphene. But often it hasn’t necessarily been performed using the proper framework, so many of these tests need to be redone. We share the cost of outstanding tests with other members of the consortium. It’s a ‘one substance, one registration’ policy that means we don’t have to duplicate unnecessary testing.
The registration for manufacturing/importing 10 tonnes of a substance per year is around €10,000-80,000. But as you extend this to more than 1,000 tonnes per year, you could be talking about several million Euros per registration. We want to share that cost as an industry rather than companies going it alone.
What happens when you add functional groups to graphene or want to explore other 2D materials?
Adding chemical functional groups to the edges of the surface of graphene is hugely beneficial in some applications. However, this may bring about very different toxicological profiles of these substances which need to be studied if they are to be manufactured at scale.
There are also thousands of other layered or 2D materials beyond graphene that haven’t been considered for registration yet. Just getting graphene to this point has been a long process as a registered material in industrial quantities, and other novel nanomaterials will undoubtedly lag behind.
You were recently given the Rising Star in Industry award by the Royal Society of Chemistry. Tell me how that came about and what it was like to win…
It was fantastic to win and pretty unexpected! My peers nominated me for my leadership role in trying to get the industry to work together. In the graphene REACH registration consortium, I lead the technical working group, which provides advice and help to other graphene manufacturers to characterise and test their materials in the same way. If we’re all using different tools to measure graphene and analysing samples differently, you’d get a wide distribution of properties. We’re trying to standardise things as much as possible.

Versarien is a member of The Graphene Council, and I’m a strong supporter of what they are doing for the industry. They’ve done some great work recently in creating a graphene classification framework for the industry and engaging with United States bodies like the Environmental Protection Agency for export to US markets. We want to make sure that what we do in Europe can be applied or can be adopted by the US.
Versarien was awarded ‘Verified Graphene Producer’ status at The Graphene Council’s recent conference in Birmingham. Why is that important?
Versarien has been a “Verified Graphene Producer” since 2019. We are the only graphene company to achieve the re-verification that was awarded to us in Birmingham.
The Graphene Council is one of the only companies in the industry to offer such a verification. We quickly adopted it because we saw the value of having something to separate us from our competitors and certify that we can produce what we claim to be selling.
To achieve this, The Graphene Council takes samples of your graphene material from the production line, audits your quality control processes and how you assess your materials once produced, and ensures everything is robust and traceable. Those samples are then taken away and tested independently to confirm what we say on our data sheet is correct. In 2019, Versarien products were first tested in the UK’s National Physical Laboratory (NPL). The recent re-verification process had our samples tested in the US.
It’s not an easy process to go through, and it will be good to see more companies go through it because, ultimately, it gives confidence to the supply chain.
You have a role on the Advisory Board of the Graphene NOWNANO Centre for Doctoral Training (CDT). What does that entail?
My involvement with CDTs started when I was a teaching fellow on the Graphene Technology CDT at the Cambridge Graphene Centre at University of Cambridge. I know the importance of nurturing that young talent, and it’s a great pool of potential future employees for our business. Graphene is a young material and the workforce is young as well. So we want to harness that knowledge that students have been developing.
As part of the NOWNANO CDT advisory panel, it is very much about understanding the output of the CDT and offering suggestions to where improvements can be made. The advisory board also comprises other GEIC partners and industry-leading experts, which also helps us broaden our networks.
We are also involved in sponsoring CDT events, a couple of our staff – former Manchester PhD students – recently presented at the CDT 2D Conference 2022 in Cheshire, showing the current cohort what can be achieved, where their career progression could lead and what it’s like to work in the industry following a PhD in graphene and 2D materials.
If we spoke again in 2, 3 or 5 years’ time, what do you think will have changed over that time in the graphene industry?
Working in such a fast-paced, innovative industry means it’s really tough to predict what’s going to happen – I think we’ll see continued adoption of graphene into many industries but we still have a big challenge around educating the public about what graphene brings to these different industries and products.
The other challenge is the demand for graphene that we could see. In the construction sector, demand for graphene could potentially be in the hundreds of thousands of tonnes per year within the next few years. But we’ve still got that gap to bridge with the regulations and registration cost, which will involve the industry working together. It’s a big enough pie for everyone to get a share, but companies will need to join forces and work together to produce the relevant materials at scale so everyone benefits.
Adoption now is mostly industrial graphene nanoplatelets in powder or dispersion form. But I think that will change. We’re starting to see the work that the Graphene Flagship has been doing with CVD [chemical vapour deposition] materials and the development of their experimental pilot line for 2D materials, which are really starting to take off in applications like sensors, optoelectronics and telecommunications.
We’ve seen issues with the semiconductor industry and chip shortages in the last year, which presents an opportunity for graphene adoption to provide new use cases and enabling technologies. I think this is where we’ll see graphene enabling new possibilities.
Find out more about Steve’s work and the wider company at versarien.com.